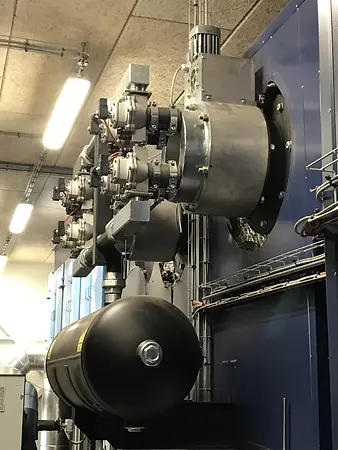
Compressed Air Soot Blower
Aerovit Type R – rotating system & Aerovit A75 – Surface cleaning

Aerovit Type R – rotating system
About Aerovit Type R
In view of the tight space conditions on some boilers and the possibility of delivering cleaning equipment to water tube boilers, we have designed a rotating soot blower, Aerovit Type R.
The system is installed between two tube sections. Its main advantages is that it requires less exterior space and allows an automatic 360° rotation with powerful blasts of compressed air which cleans every inch of the boiler sections.
Design of each unit is performed by Aerovit A/S, according to the data related to the specific application.
Data needed: fuel, boiler type, temperatures of the flue gas, drawing with dimensions of the boiler construction, photos of the boiler, measuring and photos of the space around the boiler.
Application:
The rotating unit should be placed parallel to the tubes of the boiler. The temperature of the flue gas should be kept at a constant low level. If the temperature of the flue gas increases, the duration of the cleaning cycle should be reduced until the temperature is kept at low level.
The ash and soot deposits in the boiler construction should be dry and removable. If they tend to be sticky or melting, the cleaning effect may go down.
The flue gas should not contain particles and gasses hazardous to standard steel alloys. Should condensation of corroding gasses take place, the rotating pipe unit will eventually be destroyed and must be replaced.
Maximum length of the rotating pipe unit is 2,5m. The distance between the tube banks is recommended to be min 600mm. A 290mm inlet hole is needed for flanging the Type R to the heat exchanger.
Characteristics:
Each unit has 4 pieces Aerovit valve units with built in patented features – connected to 1 piece 150 liter compressed air receiver. An electrical PLC will operate the cleaning cycles and the activations of the valves. The PLC can operate up to 6 rotating units.
​
1 cleaning cycle= 120 min. = 10,8 Nm3 compressed air. Operating pressure > 8-9 bar. Operating temperature inside the boiler construction (flue gas): < 400°C*
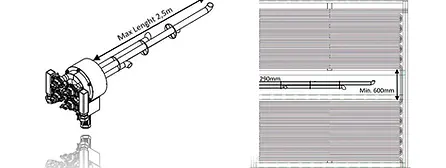
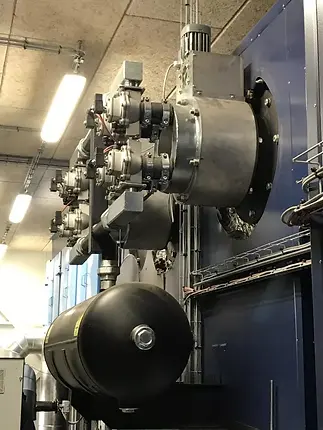
Scope of delivery:
-
1 piece rotating unit with electric motor – including 4 Aerovit valves 11⁄2”
-
1 piece rotating pipe unit with 4 pipes Ø 60 mm – replaceable blowing pipes.
-
1 piece compressed air receiver 150 liter – with manometer and safety valve.
-
1 piece air inlet – with filter/regulator, 3-way valve and non return valve.
-
1 piece electrical controller with PLC.
-
1 set of cabling between controller and rotating unit.
Aerovit A75 – Surface cleaning
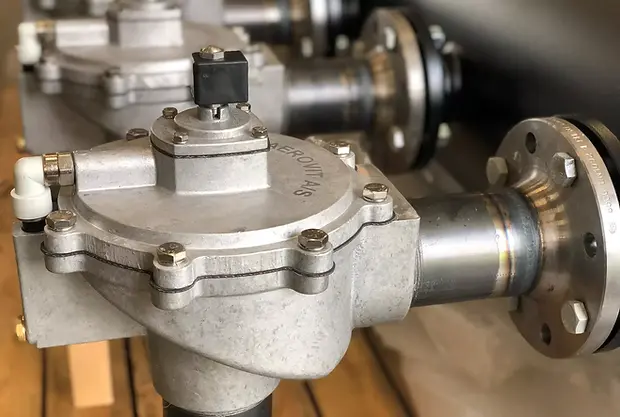
Surface cleaning
The Aerovit A75 valve helps our customers to keep the tube plate clean. At the inlet of the convection part the tubes sometimes tend to clog over time. This increases the velocity of the flue gas in the open tubes of the convection part and therefore decreases the efficiency.
​
After a while it is necessary to stop the boiler and remove the blockage. For less downtime of the boiler we can install the A75 valve for preventing this build up at the inlet of the tubes.
​
Our biggest valve is a 3” valve and with a bypass valve for keeping the valve clean before activation.
The Aerovit A75 valve can also be used for cleaning larger surfaces as water tube screens or water tube passes.
In Partnership with
